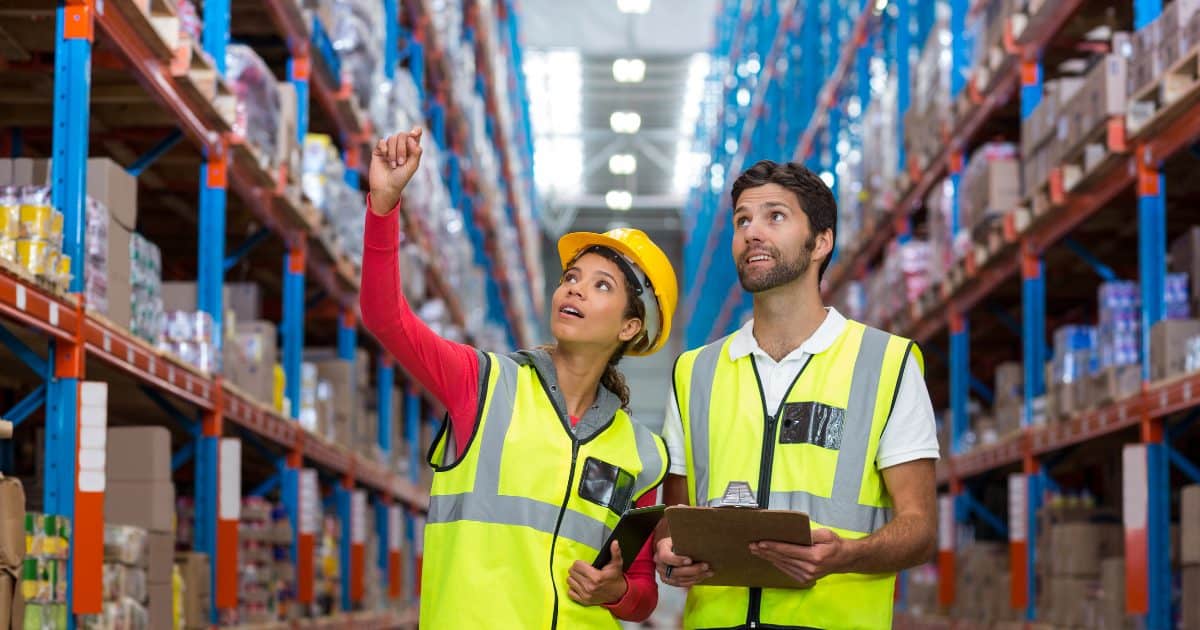
Many storage facilities tend to underperform because they’re not familiar with the principles of design and operations in warehousing. While learning the principles does not automatically guarantee your warehouse business will find success, it will undoubtedly help you plan your facility better to optimize your operations.
The following are some of the most important rules you need to know and understand when it comes to designing and running a distribution center:
Aim for Minimal Touches of the Goods
When you say “touch the goods,” it means picking up a box of goods and putting it down on a forklift or the floor when you rest. Ideally, there is zero touching of the goods for maximum efficiency, but that only happens in an automated warehouse because machines don’t get tired.
A realistic goal for manually operated warehouses is to minimize the number of touches to three or four. If you cut down on unnecessary stoppages, you’ll improve the overall efficiency of cargo movement.
Utilize a One-Way Flow
Another way to increase efficiency inside the warehouse is to utilize a one-way system for the lift trucks. By sticking to a one-way plan, you can pick a path through the warehouse that allows your workers to maximize their time and effort. There would be no chances of truck traffic as long as you’re running track adjustments for each worker, plus it would be easier for truck drivers to back into a dock or reverse directions if the spaces are secured in a singular direction.
Ensure that Stocks are in the Right Place
There are two types of product slotting in the warehouse business: triadic and non-triadic. A triadic warehouse sorts its goods into three categories: (1) fast-moving products, (2) medium moving product, and (3) slow product. Ideally, you should organize your warehouse using a triadic system so that you can better prioritize which items should be picked up first.
If you’re running an automated warehouse, you have no choice but to work with a non-triadic system. That’s perfectly fine; however, since the computerized machines don’t really need to know where the stock is, all they need is for someone familiar with the products to operate the crane, the storage systems, and the retrieval systems.
Keep Only the Right Amount of Stock
It’s important to have the right amount of stock for your warehouse. Many times, people tend to prioritize the sales value of the stocks more than the movement capabilities of the product, leading to wasted space if the demand suddenly decreases. When deciding how much stock to get for a particular product, check how fast it can be moved so you can how the logistics part turns out. While you should still look at the sales value, considering the volume of goods is always the smarter priority.
Labor Should be Done Efficiently
To maximize resources, labor should be optimized in all warehouse operations. To monitor if your workforce is being efficient, measure the time put into the warehouse operations and the actual work output. If you can increase labor efficiency, it would do better for the business since it means that the same amount of labor will produce higher output.
Use the Correct Materials Handling System
When identifying stocks for inventory purposes, you call them stock-keeping units (SKUs) for the space they occupy. Companies are currently increasing the range of products that they can hold to maximize storage space and stay competitive in the warehousing industry. However, whenever you increase the number of SKUs, you also need to modify your logistics operations because you can’t expect the same physical workflow to handle a higher volume of goods and stay efficient.
If you’ve got a low volume of SKUs, you can use a simple materials handling system for the job. Now, if you plan to increase your SKUs, you might want to consider adding a medium level of mechanization to increase efficiency. Choosing the suitable materials handling system for your volume and workload is necessary to maintain maximum productivity.
Consider Using Warehouse Management Software
Using management software can help you make decisions more easily when complications arise in warehouse operations. The management software can also lessen the difficulty of monitoring daily tasks by distributing tasks evenly and tracking the time it takes for each job to complete. The information that is generated can then be used for better resource planning and management.
A Final Word on Warehousing Principles
When you design your warehouse and plan operational tasks, it is crucial to think about multiple facets of the job to ensure that you have several options if something unexpected comes up. Always consider remote possibilities when planning warehouse operations to improve your business’s resilience and adaptability.
Making mistakes in warehouse design can be costly, so it’s essential to be as careful as possible. If you need assistance in figuring out how to operate a warehouse best, you can contact Wholesale Industrial Parts for professional advice. Wholesale Industrial Parts has more than 75 years of experience in the warehouse industry and can guide you through the business while ensuring you get only the top-quality material handling equipment.