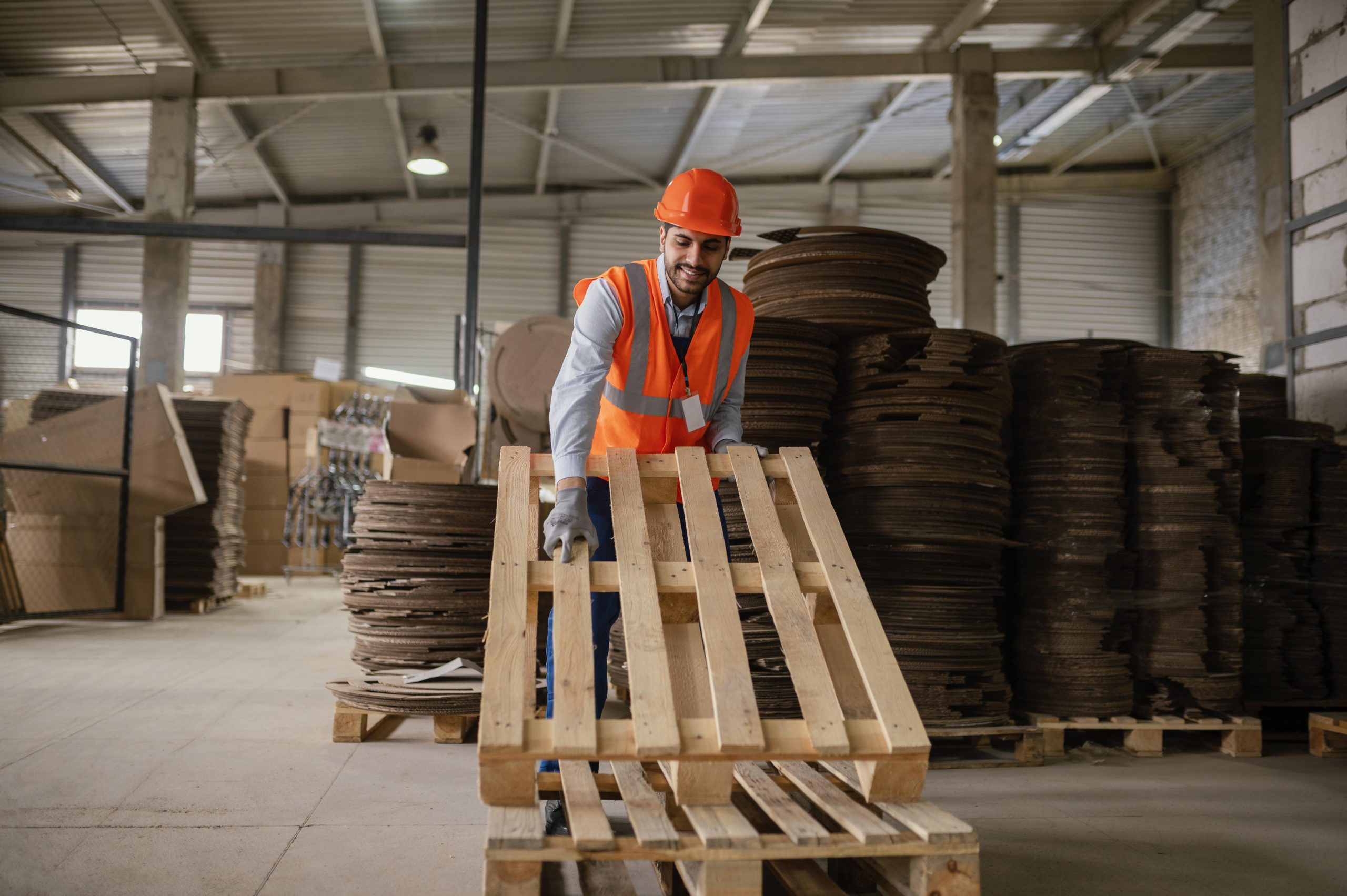
Efficient material handling is crucial in today’s fast-paced industries, but it shouldn’t be at the expense of your employees’ well-being. This is where the science of ergonomics comes in, as it focuses on designing workplaces, equipment, and tasks that accommodate the human body’s capabilities and limitations.
Join us on a journey to transform your workplace into a comfortable and efficient haven where everyone can thrive. Keep reading!
Common Challenges in Material Handling
Material handling is an indispensable aspect of numerous industries, but it’s not without its share of challenges. From the risk of musculoskeletal disorders to productivity bottlenecks and safety concerns, these hurdles can impede your workforce and operations.
Musculoskeletal Disorders (MSDs)
Musculoskeletal Disorders (MSDs) are among the most prevalent and significant challenges in material handling workplaces. These disorders encompass a range of conditions affecting muscles, tendons, ligaments, and other musculoskeletal structures.
MSDs are often caused by repetitive motions, awkward postures, and overexertion, all of which are commonly encountered in material handling tasks. Some examples of MSDs include:
- Back Pain: Employees frequently lifting heavy objects or bending improperly are at risk of developing chronic back pain.
- Carpal Tunnel Syndrome: Repetitive tasks like gripping tools or handles tightly can lead to carpal tunnel syndrome, characterized by wrist pain and numbness.
- Tendonitis: Tasks that involve repetitive movements can cause inflammation of tendons, leading to conditions like tendonitis.
Productivity Issues
Productivity is another critical concern in material handling workplaces. Inefficient processes can result in a host of issues, such as:
- Delays: Slow material handling can lead to delays in production or shipping, impacting the entire supply chain.
- Wasted Time: Employees spending excessive time on tasks due to poor workspace design or inadequate tools can be highly unproductive.
- Errors: Rushed or fatigued workers are more likely to make mistakes, leading to rework or product defects.
Safety Concerns
Safety should always be a top priority in material-handling workplaces.
And safety concerns can arise from various factors, including:
- Trips and Falls: Cluttered work areas, uneven surfaces, and inadequate lighting can contribute to slip, trip, and fall accidents.
- Equipment Hazards: Unsafe use of material handling equipment, like forklifts or pallet jacks, can result in serious accidents.
- Overexertion: Employees attempting to lift or carry objects beyond their capacity are at risk of injury.
Ergonomic Principles in Material Handling
Incorporating ergonomic principles into material handling can reduce injuries, improve safety, increase productivity, and boost employee satisfaction, ultimately contributing to long-term success. Let’s explore how these principles can help create safer and more comfortable workplaces.
Proper Body Mechanics
Lifting Techniques
One of the fundamental aspects of material handling is lifting objects, which, when done incorrectly, can lead to serious musculoskeletal disorders (MSDs). It’s important to use proper lifting techniques guided by ergonomics to avoid this issue, including bending at the knees, keeping the load close to the body, avoiding twisting while lifting, and using leg muscles instead of the back. Training employees in these techniques can significantly reduce the risk of back injuries and strains.
Carrying Techniques
Carrying materials is another routine task in many workplaces, and ergonomics promotes balanced carrying techniques. Employees should also be encouraged to use tools like carts, dollies, or conveyors when handling heavy or bulky items. This not only reduces the physical strain but also improves efficiency.
Workspace Design
Workstation Layout
Your workstation’s layout can have a profound impact on the ease and safety of material handling tasks. Ergonomics emphasizes arranging workstations to minimize unnecessary movements and reduce the risk of overexertion or injury. Materials should be placed within easy reach to eliminate the need for excessive bending, stretching, or twisting.
Storage and Shelving
Ergonomic principles extend to storage solutions that promote both safety and efficiency. Adjustable shelving and storage systems can accommodate different sizes and weights of materials, reducing the need for awkward reaching or heavy lifting.
Tools and Equipment
Ergonomic Tools
Ergonomically designed tools are engineered with the user’s comfort and safety in mind. They have features such as cushioned handles, reduced vibration, and proper weight distribution to minimize hand fatigue and repetitive strain injuries.
Material Handling Equipment
Forklifts, pallet jacks, and conveyor systems are essential material handling equipment. Ergonomic considerations in their design can greatly improve safety and efficiency. Features like adjustable seats, controls, and lifting mechanisms ensure that operators can work comfortably while minimizing the risk of accidents.
Training and Education
Employee Training
Proper training in ergonomic practices is key to successful implementation. Educate employees on the importance of ergonomics, how to use ergonomic tools and equipment, and safe lifting and carrying techniques. Regular reminders and refresher courses can help reinforce these principles.
Supervisor Training
Supervisors play a critical role in ensuring that ergonomic principles are followed consistently; hence, they should also be trained to recognize ergonomic issues and address them promptly. In addition, they can lead by example and encourage a culture of safety and ergonomics within the workplace.
Implementing Ergonomic Changes
Implementing ergonomic changes in material handling is not a one-time fix; it’s a commitment to continuous improvement and a culture of well-being.
Assessment and Evaluation
Identifying Problem Areas
Before any ergonomic changes can be made, take time first to identify problem areas within your processes. Key steps include:
- Worksite Analysis: Conduct a thorough analysis of your work environment. Look for areas where employees may be at risk of injury or discomfort due to poor ergonomics. For example, you could examine workstation layouts, observe material handling tasks, and assess equipment usage.
- Injury and Incident Records: Review historical injury and incident records to identify patterns or trends related to ergonomics. This information can help pinpoint areas where ergonomic improvements are urgently needed.
Gathering Employee Feedback
Employees who perform material handling tasks are invaluable sources of information, and their input can uncover issues that may not be immediately obvious to management. Encourage them to provide feedback about their work experiences and any ergonomic challenges they encounter through surveys, focus groups, or one-on-one interviews.
Designing Ergonomic Solutions
Workspace Redesign
Based on the identified problem areas and employee feedback, redesign workspaces to align with ergonomic principles.
This may involve:
- Layout Optimization: Reconfigure workstations to minimize unnecessary movements and reduce ergonomic risks. Place materials within easy reach so employees don’t need to bend, stretch, or twist excessively.
- Adjustable Furniture and Equipment: Invest in furniture and equipment customizable to fit individual employees’ needs. Adjustable chairs, height-adjustable work surfaces, and ergonomic accessories (e.g., keyboard trays) can accommodate various body types and preferences.
Equipment Upgrades
Upgrade equipment and tools to ergonomic versions to reduce physical strain and discomfort.
You may want to check out the following:
- Ergonomic Tools: Replace standard tools with ergonomically designed alternatives that feature cushioned handles, reduced vibration, and improved weight distribution to minimize hand and wrist fatigue.
- Material Handling Equipment: Invest in ergonomic material handling equipment such as pallet jacks, forklifts, and conveyor systems with features like adjustable seats and controls for operator comfort and safety.
Implementation and Testing
Pilot Programs
It is advisable to introduce pilot programs to a specific area or department before implementing ergonomic changes throughout the company.
This step allows you to:
- Assess Feasibility: Determine whether the planned changes are practical and effective in a real-world setting.
- Gather Feedback: Collect feedback from employees involved in the pilot program to make necessary adjustments before full implementation.
Monitoring Progress
Once ergonomic changes are implemented, the work isn’t done. Continuously monitor progress such that changes are achieving the desired outcomes.
- Regular Audits: Conduct periodic audits to assess the effectiveness of the ergonomic improvements and identify any new issues that may have arisen.
- Employee Feedback: Maintain an open channel for employee feedback. Encourage them to promptly report any discomfort or concerns and use this feedback to make ongoing adjustments and refinements.
Regulatory Compliance
Regulatory compliance in material handling workplaces guarantees the safety of employees, prevents accidents, and avoids legal consequences. Familiarizing yourself with local regulations like OSHA and international standards relevant to your industry is a vital move toward creating a compliant and safe material handling environment.
OSHA Guidelines and Regulations
The Occupational Safety and Health Administration (OSHA) is a key regulatory body in the United States responsible for setting and enforcing workplace safety and health standards. In the context of material handling, OSHA provides specific guidelines and regulations that employers must adhere to in order to maintain a safe and compliant workplace. Employers should regularly review OSHA guidelines, provide training to employees on relevant regulations, and conduct internal audits to ensure compliance.
International Standards
In addition to local regulations like OSHA in the United States, there are international standards and guidelines that can provide valuable insights and best practices for ergonomic and safety considerations in material handling. While these international standards may not be legally binding in all jurisdictions, they are widely recognized and respected in the industry. Examples include ISO 11228 (Ergonomics – Manual Handling), ISO 9001 (Quality Management System), and ANSI/ITSDF B56 Standards (Industrial Truck Standards Development Foundation).
Understanding and adhering to international standards, where applicable, can enhance the safety and efficiency of material handling operations, especially for organizations with global operations or export/import activities.
The Undeniable Benefits of Ergonomic Improvements to Your Material Handling Workplace
Investing in ergonomic improvements not only protects your workforce but also enhances your bottom line. By implementing the ergonomic principles outlined in this blog, you can prioritize your employees’ well-being while improving your operation’s efficiency. Your dedication to ergonomics will ultimately pay off in the long run.
Wholesale Industrial Parts stocks a vast inventory of material handling parts that will help maintain the excellent working condition of your equipment. We take pride in sourcing the parts you need at competitive prices and providing exceptional customer service. You can reach us at (844) 588-8455 or info@wiparts.net. We simplify the buying process for you so your operations will keep running seamlessly!