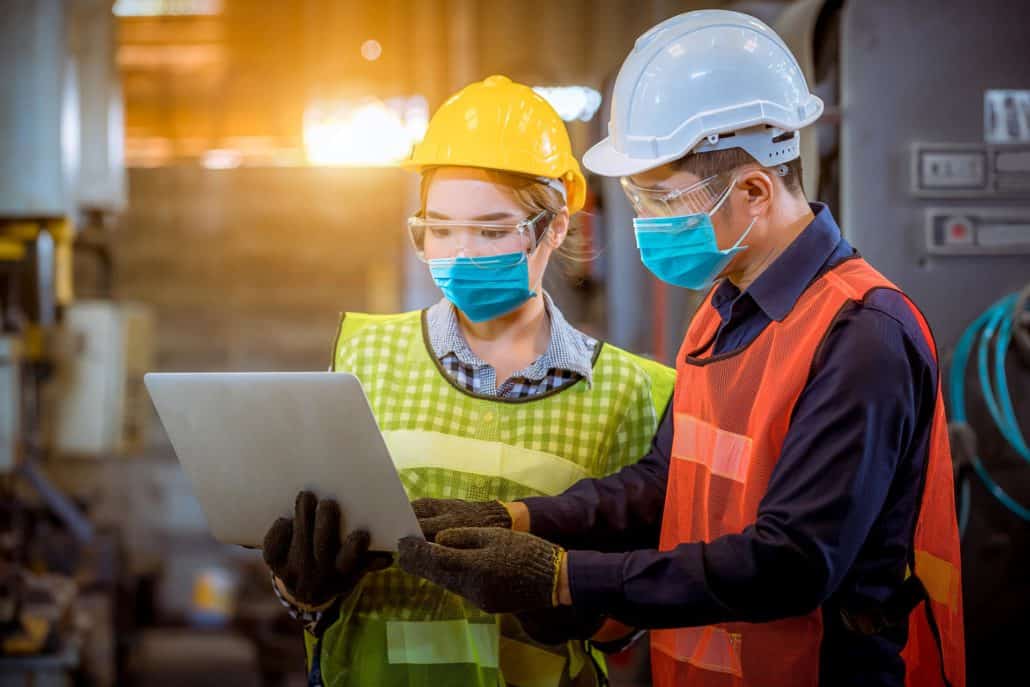
Historically, the warehouse industry has one of the highest worker injury rates in the private sector, with surveys showing that for every 100 full-time employees, the accident rate is around five. This is a worrying trend as the warehouse and storage sector is continuously growing due to the new consumer behavior brought upon by the pandemic.
According to a recent survey conducted by the US Bureau of Labor Statistics, there are more than 1.25 million workers in the storage and warehouse sector, a trend that is expected to continue in the next coming years due to the growing popularity of e-Commerce and deliveries.
Aside from ethical reasons, promoting warehouse safety is important to improve productivity and reduce costs such as worker’s compensation and premise liability lawsuits.
Related blogs:
- What Wholesale Industrial Parts Can Do For You
- How Do I Improve My Warehouse Organization and Layout?
- Best Warehouse Safety Practices: A How-To Guide
Wholesale Industrial Parts, a company that sells replacement parts of warehouse vehicles and equipment, shares some tips on how to promote warehouse safety.
Eliminate or at least reduce fire hazards.
Warehouse supervisors should conduct regular training and inspection to ensure that all workers know the fire safety measures. In addition, the facility must have fire alarms, sprinklers, extinguishers, and other similar equipment.
Other ways to reduce fire hazards:
- Keep clutter to an absolute minimum because they can fuel the fire and hamper access to emergency exits.
- Use and store chemicals responsibly.
- Keep all the machinery and electrical equipment in good working condition to prevent short circuits and overheating, which are the common causes of fire.
- Workers should not smoke during warehouse operations; smoking should only be allowed in a designated area.
- Ensure easy access to all fire alarm equipment and electrical control panels.
Reduce cutting hazards.
Warehouse workers handle packing and unpacking tasks that require knives, cutters, and scissors. To reduce cutting risk, the use of safety knives and personal protective equipment or PPE is imperative.
In addition, all the workers should receive safety training that includes proper cutting techniques.
Keep the floor area safe.
Remove potential hazards like stray cords, spilled liquid, cracks, and debris on the floor. The goal is to prevent slip and fall accidents and machine/equipment damage.
Ensure proper storage.
Again, proper training is the key to prevent most warehouse accidents such as falling objects. The general rule of thumb is to place heavier loads on the lower shelves, while long and top-heavy items should be laid on their side and/or secured correctly to prevent tipping over.
Improper placement and storage can result in falling objects, potentially causing worker injuries and damage to equipment or any property.
Ensure adequate ventilation.
While any warehouse company needs good ventilation, this is particularly important for facilities that handle dangerous chemicals that pose risk of inhalation, dizziness, and respiratory illnesses. To further reduce the risk, workers should also receive proper training in handling, storage, and disposal of these products.
Promote proper ergonomics in the workplace.
Warehouse employees do a lot of heavy lifting, which makes them susceptible to fatigue and muscle strain. To prevent workplace injuries, they should receive ergonomics training that includes proper posture and lifting.
Installing equipment that promotes ergonomics such as anti-fatigue mats is another way to reduce work-related injuries.
Install signages and warning signs.
Warehouse and stock rooms should meet the required health and safety standards which include installing universally recognized safety symbols.
Ensure safe charging stations.
Charging and refueling stations are prone to fire and explosion because they often carry gasoline, petroleum gas, and other flammable products. To reduce such risks, they should be away from open flames, and smoking should be prohibited except in a safe, designated area.
Use lockout/Tagout (LOTO) programs.
LOTO ensures that all energized equipment is shut off to prevent workers from being electrocuted or caught between moving mechanical parts. To further minimize the risk, they must receive training on applying and removing LOTO equipment after maintenance work.
Promote awareness during warehouse operations.
Even rudimentary forms of communications like yelling one’s location and direction are enough to reduce worker injuries and accidents caused by collision and slip and fall.
Identify high-risk areas and tasks.
Historically, the docks and the area where the forklifts operate are the most high-risk areas in the warehouse and storage sector. To prevent accidents, companies should only hire competent forklift operators who have completed certified training and continuously undergo refresher training.
To further minimize the risk of accidents, there should be warning signs to prevent people from getting near docks and forklifts.
Proper maintenance of forklifts can also reduce accidents. A good rule of thumb is to have them serviced every 200 hours of use to ensure that the rotors, spark plugs, lift, and tires are all working properly.
If you need replacement parts for your forklift and other warehouse equipment, contact Wholesale Industrial Parts at (844) 588-8455. We are a Sacramento-based company that sells and ships forklift parts anywhere.